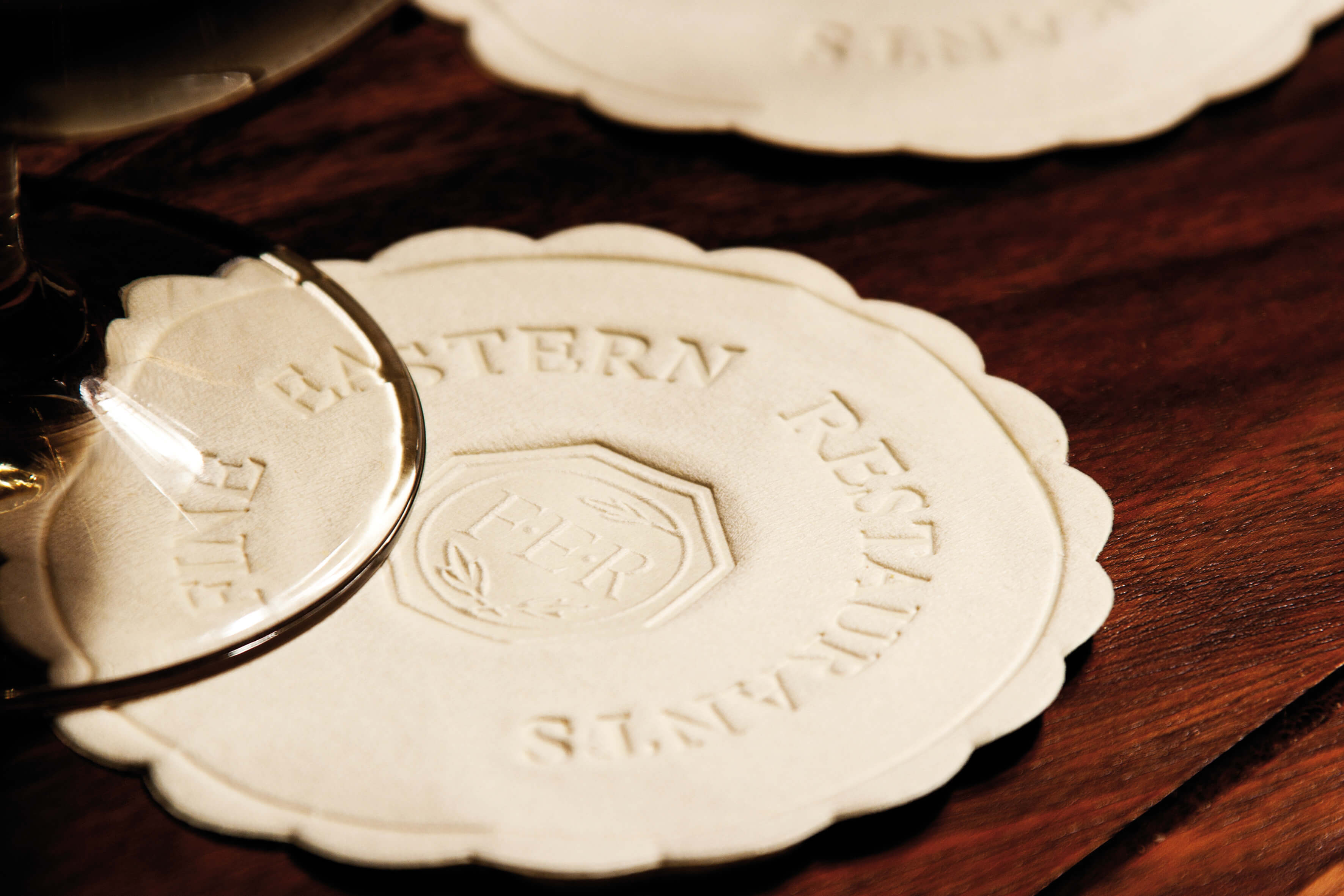
We like to say that style begins with the smallest details. The tissue and paper products that you present to your customers, while they may seem like a small touch, can go a long way to enhance the value of your brand, make your brand memorable, and offer a bit of extra refinement. If they are done properly.
A big part of a well-done paper product is choosing the best printing method to reflect your brand and your service. But if you’re not familiar with the print industry, it may be tricky to understand the different printing methods available to you. We encourage you to use our helpful guide as a resource for selecting the printing method that best fits your style.
Popular Printing Methods
Offset Printing
Using the offset printing process, your logo or approved design image is replicated onto a printing plate. Ink is applied to the plate and only the image holds the ink. During the actual printing process, the image is transferred or “offset” onto a rubber blanket and then onto the chosen printing surface.
To print a four-color design and achieve your unique brand colors, four printing plates are used, each holding a single color (black, cyan, magenta and yellow). These colors are layered at specific percentages until the desired color is achieved.
Offset printing can be used for both “short runs” (low print quantities) and “long runs” (high print quantities). Offset can produce photo-quality print results and double-sided printing is possible.
Flexographic Printing
The flexographic (or flexo) printing process get its name because the image to be printed is placed on “flexible” printing plates, usually made of rubber. The plate is inked and transferred onto the printing surface.
Just as with offset printing, a four-color print is created by using four flexo plates, each holding a different print color. The prints from each plate are layered to create the approved color and design.
Flexo printing is recognized for its quick production process.
Letterpress Printing
Letter press printing takes us back to the origins of printing. In this printing process, blocks containing a letter or an image are inked up and paper is pressed into the blocks, using heat and pressure. Used to produce a more sophisticated and luxe presentation, letterpress printing creates an embossed look, meaning the printed image is raised on the printing surface, adding dimension.
There are two additional options for finishing off your embossed printing, beyond simple ink embossing.
Foil Embossing – Using this method, the embossed design is set off by a metallic foil. Foil embossing applies a gold or silver foil through heat and pressure.
Blind Embossing – Using a blind emboss method, no ink of foil is added to highlight the embossed area. The image and words are the same color as the print surface, resulting in a very subtle presentation.
Choosing the Best Printing Method for Your Needs
To make a final decision on the print method you’ll use to produce your product, you’ll most likely need to take the following aspects into consideration: budget, paper type, and project timeline. Each of these will play a role in choosing the best printing method for each individual project.
Project Budget
Flexo printing often results in a more attractive price because of the faster production time. However, budget shouldn’t always be the main determining factor. If your brand is built upon an image of quality, premium or luxury, letterpress printing offers more exclusive printing results, but at a higher cost.
Paper Type
Letterpress and flexo printing are possible on nearly all qualities of paper, including more delicate materials like Airlaid, parchment and tissue papers. Offset is most commonly chosen for printing on cardboard beermats or paper coasters.
Project Timeline
If time is not on your side and you need a very quick turn-around on your project, you’ll want to choose the flexo printing methods because of the efficient production times. Letterpress printing, because of its intricate process, has a slower production speed but is still able to be completed in a tight timeline for small runs.